Design of Resource-Efficient Processes and Process chains for Powertrain Components
Sub-Projects
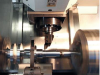
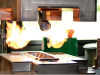
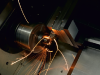
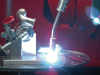
Head of Field of Action
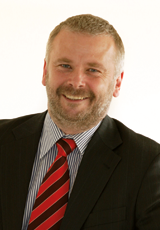
Prof. Andreas Schubert
Professorship Micromanufacturing Technologyphone: +49 (0)371 531-34580
fax: +49 (0)371 531-23549
e-mail: andreas.schubert@mb.tu-chemnitz.de
Professorship Micromanufacturing Technology
Participants
Prof. Reimund Neugebauer | President of the Fraunhofer-Gesellschaft |
Prof. Andreas Schubert | Professorship Micromanufacturing Technology |
Prof. Peter Mayr | Professorship of Welding Technology (German) |
Prof. Gudula Rünger | Professorship for Practical Computer Science |
Prof. Christoph Helmberg | Professor of Algorithmic and Discrete Mathematics (German) |
Prof. Uwe Götze | Professorship Management Accounting and Controlling |
Prof. Klaus Matthes | Professorship of Welding Technology (German) |
Prof. Frank Richter | Professorship Solid Body Physics (German) |
Prof. Matthias Putz | Fraunhofer Institute for Machine Tools and Forming Technology IWU |
Prof. Welf-Guntram Drossel | Professorship for Machine Tools and Forming Technology |
Dr. Hans Bräunlich | Fraunhofer Institute for Machine Tools and Forming Technology IWU |
Dr. Andreas Sterzing | Fraunhofer Institute for Machine Tools and Forming Technology IWU |